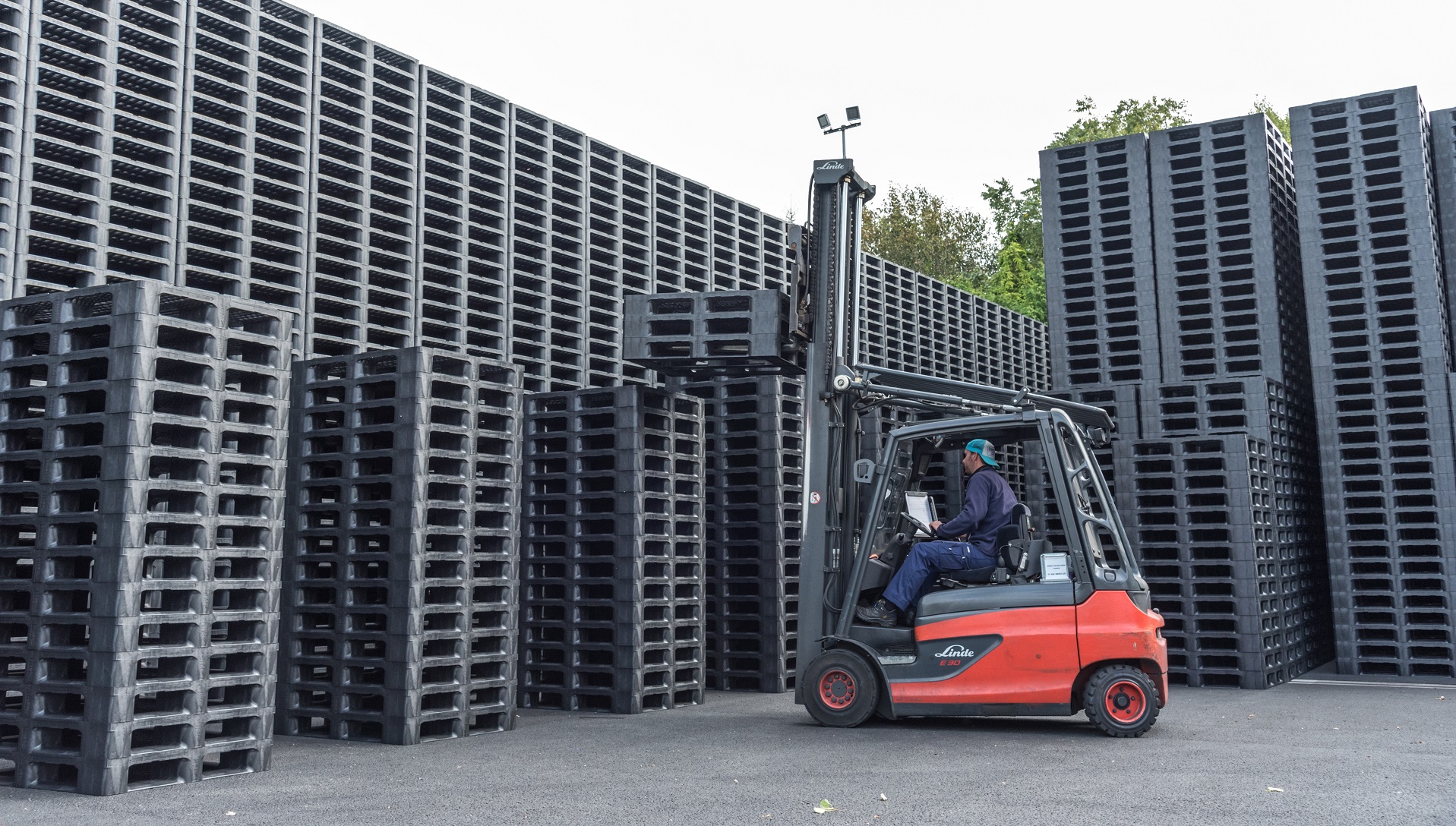
Recycled materials in AVK production
From development to production, we focus on innovation, quality and efficiency. For us, this means to consider the entire process and its impact on our society and environment.
Turning plastic waste into quality products
Decades of plastic dumping has left our nature and oceans contaminated and damaged. Luckily, we keep getting smarter in how to collect and recycle plastic waste. And once collected, either from nature or through household and industry sorting, used plastics contain various possibilities of re-entering society as valuable products.When used properly, plastic is in fact environmentally friendly. It is a solid, durable material that is easy to work with and can be used for various purposes.
Every year, +27,000 tonnes of recycled plastics find their way to our AVK production sites in Denmark and in the Netherlands - equivalent to 400 sea containers of 12 meters in length. At our production sites, the plastic gains new life as pallets and surface boxes like the ones you would find in the sidewalk or in the street. The amount of recycled plastic used in the AVK production corresponds to around 25% of the accumulated amount of collected plastic waste used by Danish households. In Denmark, AVK is now the third biggest buyer of recycled plastics.
AVK Plast in Ribe, Denmark, now also base their production on a 100% renewable energy source (wind power), which combined with their recycling efforts brings them close to a complete green cycle. They have also received the RECS certificate (Renewable Energy Certificate System), which will also strengthen their customers’ decision making when they carry out lifecycle analyses on their products.
Among many other types, the recycled plastics include soda caps and cutting waste from used airbags. When revived as a new quality product, the lifetime of the “old” plastic is extended with about 50 years.
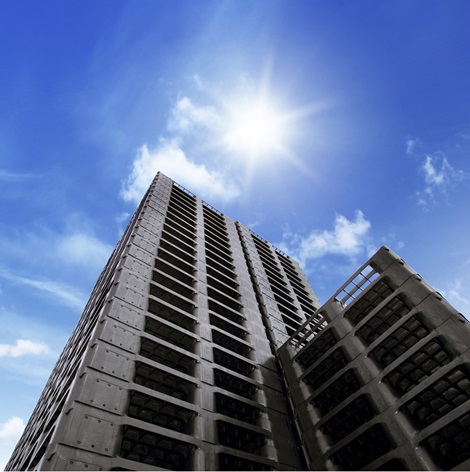
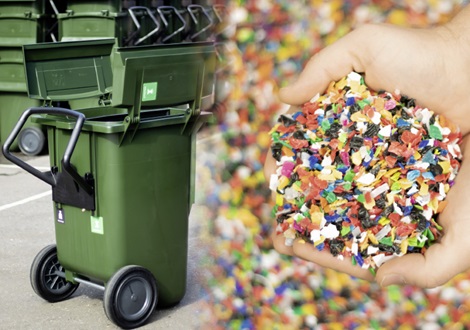
Reclaimed scrap from other industries
Regardless of which AVK foundry you visit, the result is always the same; every finished product is – almost exclusively – made from recycled iron. When casting new valves, there is a need for finding the perfect balance between new and recycled iron; always with the same high quality as the goal.Therefore, it is essential to find just the right scrap material, which can sometimes be a challenge. At AVK, we use scrap materials from the car industry and other similar industries that know exactly what their scrap consists of.
For recycled iron, it all comes down to supply and demand. If we can gather large amounts of quality scrap, we do not need a large amount of new iron. However, a percentage of new iron is always added to reach the desired features. And, regardless of the scrap source, additives such as carbon, silicon, manganese are added to obtain the correct strength.
At our foundry in China, we generally use approximately 90% recycled iron and 10% new. Other AVK foundries might use up to 30-40% new, all depending on finding scrap quality good enough for AVK standards.
Discharged cast materials in our production are always reused, and discarded products from our factories are sold locally via scrap dealers. This way, we keep our waste to a minimum. The AVK product itself is also recyclable; when dug up, after decades of use, most of the product can be taken apart and materials can be reused separately.
High efficiency and reduced environmental impact
Our Advanced Castings A/S foundry, which supplies valve, hydrant and other metal castings, uses the innovative Lost Foam method.
"Lost Foam" refers to the process of creating a foam model of the desired casting, embedding it in binder-less moulding sand and finally replacing the foam with molten metal. This opens a world of design opportunities and offers longer tooling life, as foam tooling can last for hundreds of thousands of cycles, corresponding to millions of components.
The process allows the creation of complex parts with near net shape and with no use of cores, making it possible to reduce or eliminate the material waste. Production allows low wall thickness and draft angles, which helps reduce the component weight. The sand used to embed the foam model is ceramic sand, and no use of binder is required. This makes demoulding easy, and the sand can be reclaimed to a very high degree; in general, above 99% in total. The process therefore leaves no toxic sand waste and only little dust.
The process allows an improvement in performance, which reduces the energy consumption and particle emissions into our atmosphere. Also, it helps to create a safer working environment in our production. Recycled steel scrap is the main material, constituting 85-90 % of the total melt.
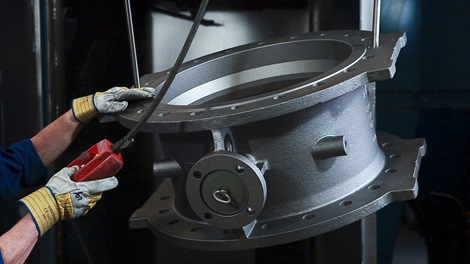
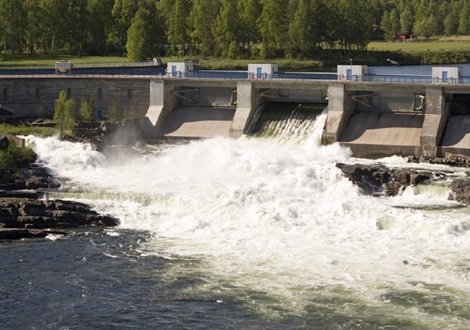
Furnes Jernstøperi: renewable energy
At Furnes Jernstøperi in Norway, there is a strong focus on protecting nature and its resources. Therefore, the company has made the decision to reduce the climate footprint by using 100% renewable energy from hydropower.
At the foundry, where many different types of industrial products are casted and moulded, energy from the nearby hydropower plants in Hallingskarvet and Hardangervidda in Norway is used. This means that the whole production runs on renewable energy. By attaching an extra guarantee of origin to the contract to the hydropower plant, Furnes ensures that all electricity used at the foundry is produced from an energy source that is 100% renewable.