
To obtain a safe and efficient water network, the piping system must be able to take in or release accumulated air. In a trial project to replace the existing air valve solution, AVK valves were tested, reviewed and approved.
Talwandi Sabo Power Project is a vital thermal power plant located in Banawala village in the Indian state of Punjab. The power plant is operated by Talwandi Sabo Power Limited (TSPL), a subsidiary of Vedanta.
The plant has a capacity of 1,980 Megawatt – enough to supply more than 400,000 homes. As per the guidelines of the Government in India, TSPL supplies 100% of the electricity to the Punjab State Electricity Board (PSEB) for 25 years. A cooling tower system is used to remove the heat from the water for reuse in condenser during power generation. Two lines are connected to the tower; as hot line (about 45-60°c) and a cold line (15-25°c).
A few air valves were installed in both lines to maintain the air breathing as per AWWA C512, but maintenance issues for the valves were reoccurring. Simply, water was spilling out from the installed air valve regularly after 5-6 months of operation. Consequently, the plant was facing issues of flooding near most of the valves and the overall efficiency of the system was declining.
On-site observation
The valves used were ball type double acting air valves, and they were leaking due to pre/post closure. Dissolved air is also creating issues as the line is typically completely filled with water and has a lot of bends and joints.
The AVK team visited the plant along with a representative from Errand Enterprises and conducted a survey and collected the required details to understand the operated air volume in the piping system and other details that can affect the operation of the air valve. After review, we suggested to install series 851/45 triple acting air valves.
AVK air valves met the requirements
TSPL agreed to install four valves (DN200) as an initial solution and wanted to review the operation of the valves for at least six months. The valves were supplied and installed in 2020. TSPL observed the operation for a year and found it satisfactory. TSPL now shared the requirement for another 20 air valves and request that we support them with an appropriate solution to replace the defective ones installed.
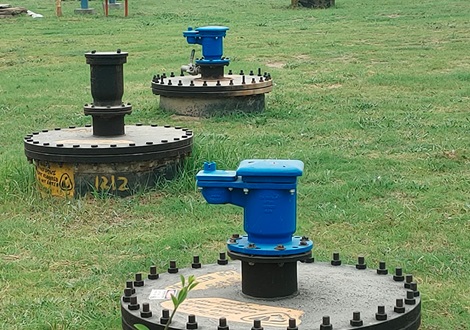
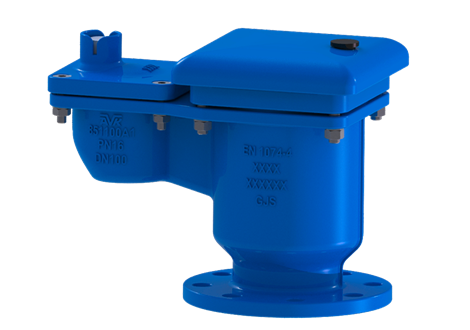
Products supplied to the project
- 4 x DN200
- 8 x DN200 - yet to be installed
- 12 x DN150 - yet to be installed
Did you know, that...?
In the absence of a suitable air valve in a water system, the following issues can occur:
- Destructive vacuum conditions
- High pressure surge
- Cavitation damage
- Lower pumping efficiency
- Inaccuracy in the measurement of fluid volumes
- The presence of air can have a detrimental effect on system drainage efficiency
- Metal parts in the system and system accessories corrode at a higher rate
- Physical risk - when large volumes of air under pressure are released at high velocities
- Reduced air pockets in the system cross sectional area, higher energy losses, tremors in the system and in extreme conditions: an entire stoppage of the flow